The Keys to a Successful Predictive Maintenance Program
Implementing a predictive maintenance program (PdM) can be an intense process. Collecting, standardizing, and analyzing data. Developing and refining predictive models. Analyzing results and documenting insights.
With so many steps, the amount of time and money invested in a PdM system can quickly add up. This is why a failed predictive maintenance can be devastating for a business. To help organizations avoid this, Sheila Kennedy laid out the top seven factors that lead to a successful predictive maintenance program in an article from Plant Services.
In it, industry professionals give their advice on creating and, more importantly, maintaining predictive maintenance programs. Below is a summary of these seven recommendations to keep PdM programs on track:
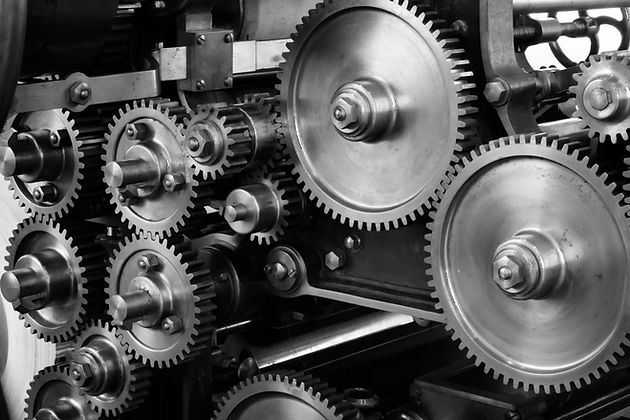
1. “Make reliability a shared vision”
Sheila Kennedy states that there needs to be a cultural shift throughout the entire company for a PdM program to receive the necessary focus and follow through. Designating a common goal shared by the entire team helps everyone recognize the importance of this program and encourage them to continue its success.
2. “It’s about people, not just the tools”
Implementing the correct tools to collect and analyze data in order to become predictive is only the first step of a PdM program. All of this technology can be useless if the team is not properly trained in predictive maintenance technologies. Having a technician whose sole job is to handle the day-to-day predictive work helps keep the program running smoothly.
3. “Think like an analyst and act on the data”
Set time aside to truly analyze the data collected. Getting to the root of the issue that is causing the equipment failures will be more beneficial in the long run for the company. It also allows the predictive maintenance program to realize its full potential.
4. “Educate and empower the leaders”
Just as it is important to have a specific team dedicated to a predictive maintenance system, it is also important to have solid leadership to guide them. Organizations must seek out who on their predictive team will make a good leader. This involves deciding who can set clear objectives, measure progress towards them, and then make the proper changes to achieve these objectives
5. “Plan ahead for champion turnover”
Finding and cultivating great leaders is what makes PdM programs successful. The downside, however, is that when these leaders succeed in their role, they often are drawn towards higher up positions which leads to high chance for turnover. Therefore, it is important to create a shared vision and culture surrounding PdM so that the team members following in their footsteps continue to run a successful program even after a leader moves on.
6. “Communicate the value clearly and persistently”
Properly collecting the results of PdM programs and highlighting their value is crucial for continuing them. Every potential failure that is prevented because of predictive maintenance must be reported and acknowledged. Doing so will not only raise the morale of the PdM team because they see the value of their program, it will also assist the senior leadership in understanding the significance of PdM. Clearly communicating the benefits will create a stronger culture surrounding Predictive Maintenance.
7. “Fight for your successful programs”
Communicating the value of PdM programs is closely related to fighting for these programs and helping team members at every level understand the importance of predictive maintenance. If changes in the business structure occur and the PdM program is at risk, these metrics can be what saves the project from deteriorating.
Hopefully these seven pieces of advice are helpful, whether you are restarting a PdM project or considering beginning an implementation. It is important to remember that the predictive tools are only one part of the project, the rest depends on the team backing up the program. By following these steps, your organization can strengthen this team and maintain a successful predictive maintenance program.